低水泥鋁鎂尖晶石質耐火澆注料是采用剛玉、特級礬土熟料、電熔或高純鎂砂和鋁鎂尖品材料為主,用低水泥技術配制而成的。該料又稱為剛玉或高鋁鎂砂尖晶石質耐火澆注料或者復合鋁鎂尖晶石質耐火澆注料。其性能優(yōu)良,在大中型鋼包上得到了應用。
組成材料和性能
低水泥鋁鎂尖晶石質耐火澆注料的組成材料,一般選擇高純或合成耐火原材料,科學級配,基質優(yōu)化,用鋁酸鹽水泥CA-70或CA-80作結合劑,并摻加a-AlO3和SiO2超微粉和外加劑。按澆注料的配合比要求,淮確稱量各種材料,外加4.5%-5.8%的潔凈水,機械攪拌振動成型,自然養(yǎng)護到期后進行烘干,然后做材料的理化性能檢驗,其試樣檢測結果如下:編號1-編號3用電熔白剛玉作耐火骨料和粉料:編號4和編號5分別用板狀剛玉和特級礬土熟料作耐火骨料,電熔白剛玉作耐火粉料,在耐火粉料中,均摻加了電熔鎂砂粉,高純鋁鎂尖晶石粉和a-A2O3超微粉;在編號3-編號5料中,還摻加少量的SiO2超微粉:結合劑用鋁酸鹽水泥CA-70其用量為3%-5%:采用聚磷酸鹽作減水劑,其用量為0.14%-0.22%。當鋁酸鹽水泥凝結過快而難以保證施工時,應摻加檸檬酸等緩凝劑:耐火骨料臨界粒徑的大小,依鋼包襯工作層厚度而定。耐火骨料與耐火粉料的質量比約為7:3:快干劑的用量,以試樣驟然放進到50℃電爐中并保溫一定時間后取出,試樣無爆裂時為宜。
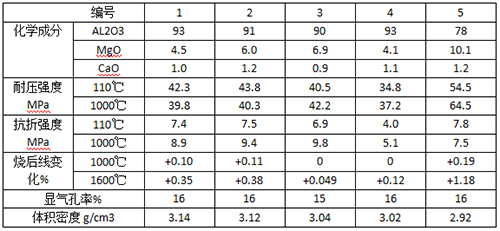
沖上表可知,低水泥鋁鎂尖晶石質耐火澆注料的性能是優(yōu)良的,1550-1650℃的燒后線變化均呈微影脹,能堵塞氣孔,緩沖因收縮而產生的裂紋,能提高抗渣性;烘干和1000℃燒后強度比值約為1,有利于烘烤。1600℃左右的強度較高,說明材料燒結了并生成新的礦物;該料的A2O3和MgO合量約為97%,說明料較純凈,不易生成過多的低熔物,其中電熔鎂砂粉中的MgO和鋁鎂尖品石帶入的MgO.其合量為4.1%-10.1%。前者能滿足生成尖晶石的需要,后者作為晶核能促進尖晶石生成和品體發(fā)育,這樣可提高耐火澆注料的抗渣性;鋁鎂尖晶石質耐火澆注料的顯氣孔率較低和體積密度較高,說明水用量適宜和顆粒組成合理,特別是基質料的顆粒組成完全地填充各類顆粒料間的空隙而獲得致密體。
基質組成對性能的影響
低水泥鋁鎂尖晶石質耐火澆注料的基質組成,主要有剛玉粉、尖品石粉、電熔或高純鎂砂粉、a-Al2O3微粉、硅微粉和鋁酸鹽水泥等。在耐火骨料材質與顆粒組成匹配的情況下,采用這些耐火粉料(含超微粉),進行嚴謹和科學的配方設計,就能制成具有良好的抑制熔渣滲透和抵制熔渣侵蝕的高技術低水泥鋁鎂尖品石質耐火澆注料,并獲得良好的使用效果。
在鋁鎂尖晶石質耐火澆注料的基質中,主要化學成分為AL2O3和MgO,還有少量的CaO等成分,眾所周知,Al2O3與M2O在1000℃時即開始生成MA,隨著溫度的升高,其反應充分,MA生成量增加,并伴有約8%的體積膨脹;同時,AL2O3與CaO(另有熔渣中的大量CaO)也逐漸生成高熔點的柱狀CA和少量CA2等,也伴有體積膨脹。這種自反應而產生的體積膨脹(又稱為自膨脹),抵消澆注料的高溫收縮后仍呈現(xiàn)微影脹狀態(tài),可使?jié)沧⒘现旅芑矣形⒘鸭y,能抵抗熱應力的破壞作用,提高抗渣性和杭剝落性。但是,基質中配料不當,體積脹縮不宜,低熔點生成物過多,均能降低澆注料的抗渣性。因此,澆注料中基質組成材料的品種和用量選擇,至關重要。